Types and Functions of Windings in Small Direct Drive Motors
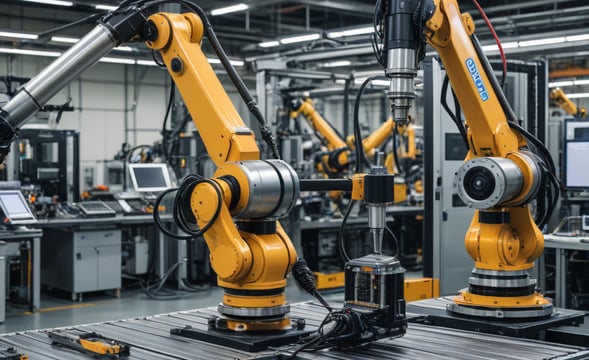
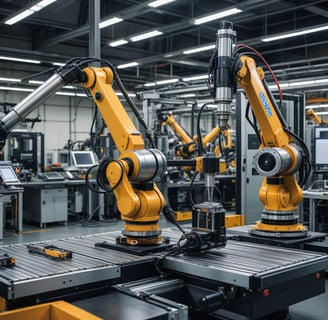
Imagine you’re designing a precision robotic arm for medical applications. Every component must work in perfect harmony, and motor performance can make or break the success of your project. One of the most critical factors? The winding configuration inside the motor. It’s often overlooked, but the choice of windings in your small direct drive motor can significantly impact its efficiency, torque, and thermal performance.
In this article, we’ll dive deep into the world of windings in small direct drive motors, exploring their types, functions, and how they influence performance in various applications. By the end, you’ll have a clear understanding of which winding configuration is right for your next project, whether it’s for robotics, automation, or precision equipment.
Why Windings Matter in Small Direct Drive Motors
Windings are essentially coils of wire wrapped around a motor's stator. When electrical current flows through these coils, it generates a magnetic field, which interacts with the motor’s rotor to produce motion. The way these windings are arranged plays a key role in defining the motor's overall performance. In small direct drive motors, where precision and efficiency are paramount, the choice of winding type can make all the difference.
Key Functions of Motor Windings:
Torque Generation: The more effective the winding, the higher the torque output for a given current.
Thermal Management: The arrangement of windings affects heat dissipation, which can prevent overheating and prolong motor life.
Efficiency: Optimized windings ensure that less energy is lost as heat, increasing overall motor efficiency.
Types of Windings in Small Direct Drive Motors
There are several winding configurations used in small direct drive motors, each suited to different performance requirements. Let’s break down the most common types:
1. Lap Windings
Lap windings are one of the most common configurations in direct drive motors. In this type, each coil is connected to the next, forming a continuous loop. This setup is ideal for motors requiring high torque output, as it allows for a larger number of poles.
Advantages:
High torque generation
Suitable for low-speed, high-torque applications
Excellent for motors with multiple poles
Applications: Lap windings are commonly used in direct drive motors for heavy-duty robotics, where torque is a key requirement. For example, TurboFlys small direct drive motors use optimized lap winding configurations for applications in industrial automation, offering the high torque necessary for precision tasks without sacrificing efficiency.
2. Wave Windings
Wave windings are more intricate, with the coils connected in a wavy pattern rather than a simple loop. This design reduces the number of poles, making the motor more suited to higher-speed applications.
Advantages:
Higher speed performance
Lower resistance, which can improve efficiency
More compact winding configuration
Applications: Wave windings are often found in motors that require both speed and efficiency. They are perfect for smaller robots where space is limited but high-speed precision is needed, such as in conveyor systems or small robotic arms.
3. Concentrated Windings
Concentrated windings focus all the coils around one part of the stator, increasing the magnetic field’s intensity in that area. This design is excellent for maximizing torque and reducing the motor's size.
Advantages:
Compact design
High torque density
Excellent for applications requiring both precision and space-saving
Applications: Concentrated windings are frequently employed in small direct drive motors where space is at a premium, like in medical devices or compact robotics. TurboFlys small direct drive motor, designed for compact robotic applications, uses concentrated windings to achieve the high torque needed in limited spaces without compromising on performance.
4. Distributed Windings
In this type, the coils are spread evenly around the stator. Distributed windings provide smoother operation, better thermal management, and reduced noise.
Advantages:
Smooth torque generation
Better heat dissipation
Reduced noise and vibration
Applications: Distributed windings are ideal for applications requiring continuous operation at consistent speeds. For instance, in precision machinery like CNC systems or high-end 3D printers, distributed windings help maintain smooth and reliable performance over long durations.
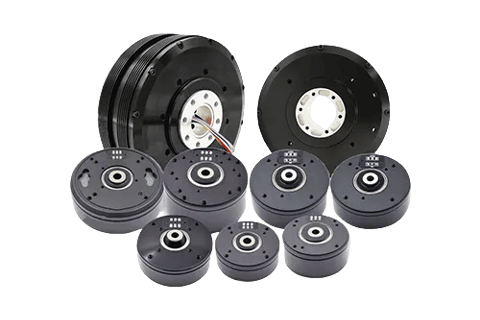
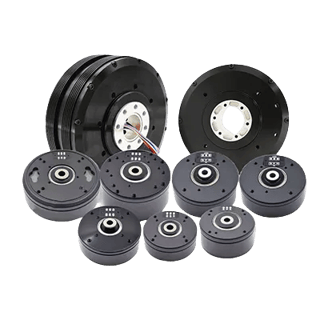
The Impact of Winding Type on Motor Performance
Choosing the right winding configuration for your small direct drive motor directly affects several key performance metrics:
1. Torque
Lap and concentrated windings excel in applications requiring high torque. If your motor’s primary role is to generate rotational force, such as in heavy-duty robotic arms or industrial automation, these winding types are ideal.
2. Efficiency
Efficiency is critical, particularly in applications where energy consumption needs to be minimized. Wave and distributed windings offer superior energy efficiency due to their lower electrical resistance and better heat dissipation, making them ideal for speed-based applications like conveyor belts or high-speed precision machinery.
3. Thermal Management
Heat management is often an overlooked aspect of motor design. Concentrated and distributed windings provide better thermal regulation, reducing the risk of overheating during extended use. For applications that demand long periods of operation, such as factory robotics, these winding types ensure durability and reliability.
4. Precision
For applications requiring high precision, such as medical devices or camera stabilization systems, distributed windings offer smoother torque output and less vibration, ensuring accurate movement without errors.
The TurboFlys Solution
When it comes to small direct drive motors, TurboFlys is a leader in providing motors that balance precision, power, and efficiency. The winding configurations in TurboFlys small direct drive motors are optimized for high torque and compact applications, making them suitable for a wide range of industries—from robotics to medical devices.
For example, TurboFlys uses advanced concentrated windings in its compact motors, delivering the perfect balance between space-saving design and torque generation. This makes them a top choice for engineers and project managers looking for reliable, high-performance motors for precision applications.
Conclusion
Understanding the role of windings in small direct drive motors is essential for choosing the right motor for your project. Whether your application requires high torque, speed, or precision, selecting the appropriate winding configuration will optimize performance and ensure reliable, efficient operation.
Whether you're designing a robotic arm or managing automation projects, consider the importance of winding types as part of your motor selection process. TurboFlys' small direct drive motors, with their optimized winding configurations, provide an excellent example of how modern engineering can meet the needs of advanced, precision-driven industries.