The Stator: Heart of the Direct Drive Starter Motor
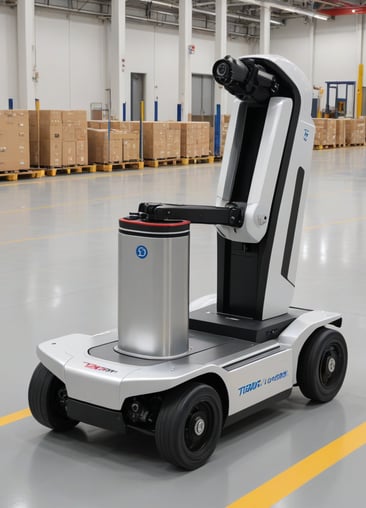
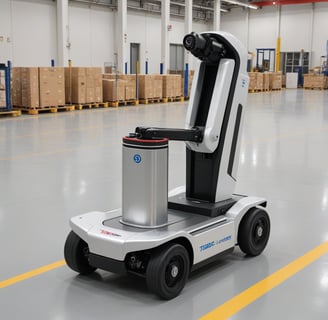
Imagine a high-performance vehicle roaring to life with just a twist of the key, the engine humming smoothly as it engages the road ahead. At the core of this seamless ignition experience lies a vital component: the stator of the direct drive starter motor. This unassuming part plays an integral role in converting electrical energy into the mechanical energy needed to start the engine, making it a true unsung hero of automotive engineering.
Understanding the Stator's Role
The stator is the stationary part of the direct drive starter motor, composed of coils of wire wound around a core, typically made of laminated steel. When electrical current flows through these coils, it generates a magnetic field that interacts with the rotor, causing it to spin and ultimately engage the engine’s flywheel. According to the Society of Automotive Engineers (SAE), a well-designed stator can improve the overall efficiency of the starter motor by up to 15%, significantly enhancing the vehicle’s starting performance.
One example of a robust design is found in the TurboFly direct drive starter motor, which integrates advanced stator technology to ensure reliable engagement even in extreme conditions. The stator in this model is engineered for durability, capable of withstanding high temperatures and vibrations that typically challenge traditional starter motors.
Technical Aspects to Consider
When examining the functionality of the stator, several key aspects come into play:
Material Composition: The choice of materials for the stator is crucial. High-quality electrical steel laminations reduce eddy current losses, leading to improved efficiency. Research indicates that using silicon steel can reduce losses by up to 50%, which translates into better performance.
Winding Configuration: The arrangement of the winding affects the magnetic field strength. More turns can enhance the magnetic field, but they also increase resistance. Engineers must find the right balance to optimize performance without compromising reliability.
Cooling Mechanisms: Given the heat generated during operation, effective cooling is essential. Some advanced starter motors incorporate cooling channels within the stator design, ensuring optimal temperature control and extending the lifespan of the motor.
Magnetic Field Dynamics: Understanding the interaction between the stator’s magnetic field and the rotor is fundamental for improving starter efficiency. This dynamic can be fine-tuned through precise engineering, which directly impacts the motor’s performance.
Conclusion
The stator may not be the most glamorous component of a direct drive starter motor, but its significance cannot be overstated. As automotive engineers and mechanics continue to innovate, focusing on the technical aspects and functionality of the stator will be vital for developing more efficient, reliable, and durable starter motors. By understanding and optimizing this crucial component, professionals can ensure that vehicles start smoothly, delivering the performance that drivers expect.
In an industry where precision is paramount, the advancements seen in products like TurboFly's direct drive starter motor highlight the importance of investing in quality stator designs. As we move forward, the evolution of starter motors will undoubtedly hinge on our ability to understand and enhance the heart of the system: the stator.