Enhancing CNC Machine Performance with Direct Drive Motors
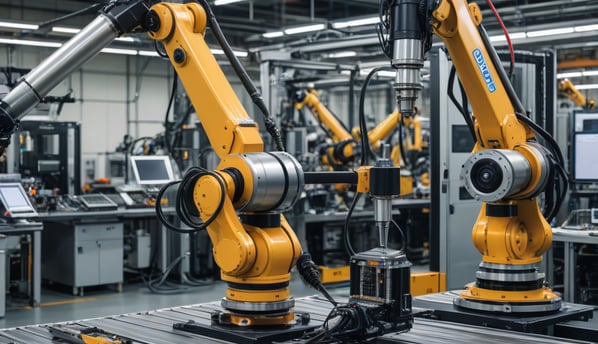
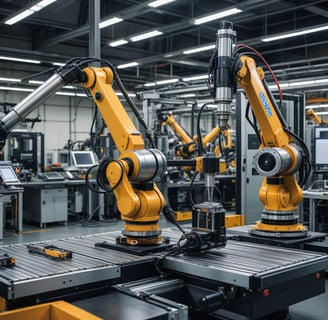
In a bustling CNC workshop, the hum of machinery is a symphony of innovation. Each spindle’s movement is a testament to precision engineering, but achieving that precision often comes down to one crucial factor: the motor. Imagine a solution that eliminates unnecessary mechanical components, reduces maintenance, and dramatically enhances accuracy—enter the brushless direct drive motor.
Why Direct Drive Motors Are Revolutionizing CNC Machines
The rise of brushless direct drive motors marks a turning point in CNC technology. Unlike traditional motors with gearboxes and belts, direct drive motors connect directly to the driven component, reducing mechanical losses and increasing efficiency. For CNC machine manufacturers, this translates to fewer moving parts, lower vibration, and unmatched precision—qualities highly sought after in modern manufacturing.
Key Benefits for CNC Applications
Enhanced Precision: Direct drive motors, such as the TurboFlys brushless direct drive motor, deliver ultra-smooth motion control, reducing positional errors and enabling tighter tolerances. Studies show that eliminating mechanical transmission can improve precision by up to 30% compared to belt-driven systems.
Improved Energy Efficiency: With fewer mechanical losses, direct drive motors consume less energy, leading to significant cost savings over time. Research indicates that direct drive systems can increase energy efficiency by 10-15%, making them a sustainable choice for CNC operations.
Reduced Maintenance: The absence of belts and gearboxes minimizes wear and tear, lowering the frequency and cost of maintenance. This ensures longer operational life for CNC machines, a key consideration for industrial procurement officers.
Higher Speed and Torque: Direct drive motors can achieve higher speeds and torque output, enabling faster machining cycles without compromising on quality. TurboFlys’ motor, for example, boasts a high torque-to-weight ratio ideal for high-demand CNC tasks.
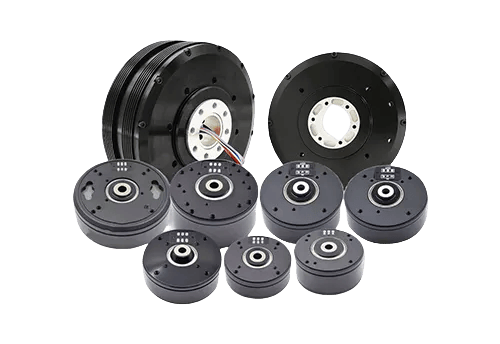
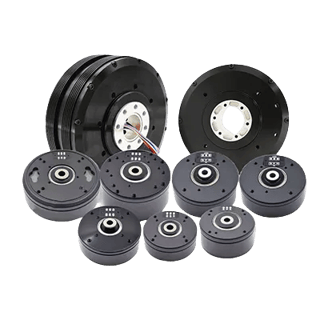
Applications in Modern CNC Machines
From aerospace to automotive, the demand for precision manufacturing is at an all-time high. Brushless direct drive motors excel in CNC applications such as:
High-Speed Milling: Achieving consistent results in high-speed operations without overheating.
Precision Engraving: Delivering flawless detail in materials ranging from metals to composites.
3D Machining: Supporting complex geometries with dynamic motion control.
What to Consider When Adopting Direct Drive Motors
While the benefits are clear, selecting the right motor requires careful consideration of factors such as torque requirements, compatibility, and cost. TurboFlys offers a versatile range of brushless direct drive motors tailored to diverse CNC applications, combining cutting-edge technology with reliability.
Real-World Impact: A Case Study
A CNC tool manufacturer integrated TurboFlys brushless direct drive motors into their latest milling machines. The result? A 20% reduction in production cycle time, a 15% improvement in energy efficiency, and near-zero downtime due to maintenance. These results highlight the transformative potential of direct drive motors in competitive manufacturing environments.
Conclusion
For CNC machine manufacturers and industrial procurement officers, brushless direct drive motors represent a game-changing upgrade. By enhancing precision, efficiency, and durability, they set a new standard in CNC performance. If you’re ready to future-proof your operations, consider exploring TurboFlys brushless direct drive motors and experience the benefits firsthand.