Enhance Gimbal Precision with High-Quality Encoders
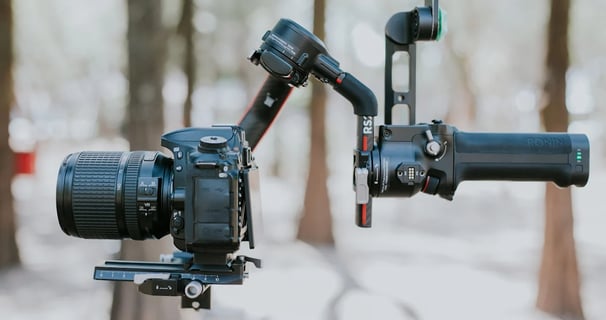
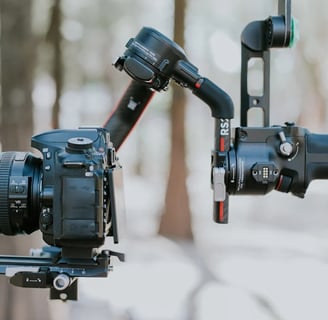
Encoders are important for improving how accurate gimbal motor encoders are. They provide instant feedback on motor position and speed, which helps control motion more precisely. Gimbal motor encoders track tiny movements to ensure motors adjust correctly, enhancing stability and allowing devices like cameras or drones to operate more smoothly. Whether using brushless motors or direct-drive systems, gimbal motor encoders deliver exceptional accuracy and dependability in motion control.
Key Takeaways
Gimbal motor encoders provide real-time feedback on motor position and speed, crucial for maintaining stability in devices like cameras and drones.
Choosing the right type of encoder—optical, magnetic, or incremental—depends on your specific needs for accuracy and environmental conditions.
High-resolution encoders track tiny movements, enhancing precision and performance, especially in challenging situations like strong winds.
Regular calibration and smart software are essential for maintaining encoder accuracy and preventing performance drift over time.
Combining load and motor encoders can significantly improve stability by correcting positional shifts quickly and effectively.
Address common challenges like noise interference and misalignment with proper installation, shielding, and regular maintenance to ensure reliable operation.
Investing in quality encoders and maintaining them properly leads to better performance and longevity of your gimbal systems.


Understanding Gimbal Motors and Encoders
The Role of Gimbal Motors in Stabilization
Gimbal motors help keep devices like cameras and drones steady. They fix unwanted movements by adjusting their position quickly. If a drone faces wind or sudden motion, gimbal motors keep the camera stable. This steadiness is needed for smooth videos or accurate flight direction.
Brushless motors are often used in gimbals because they work well and last long. They give steady performance, which is key for keeping things stable. But their accuracy depends on the feedback they get. Encoders provide this feedback, helping motors adjust correctly and stay balanced.
What Is a Gimbal Motor Encoder?
Definition and Function in Motor Control
A gimbal motor encoder is a sensor that gives important feedback about motor speed and position. It watches the motor's rotation and turns it into digital signals. These signals tell the controller where the motor is exactly. With this data, the system can make careful changes to stay stable.
Encoders also save energy by tracking movements accurately. They stop extra corrections, which helps save battery power. This is very useful for drones since power affects how well they work.
Types of Encoders: Optical, Magnetic, and Incremental
There are different types of encoders, each made for certain uses. Here are three main kinds used in gimbals:
Optical EncodersThese use light to find motion and position. They are very accurate, making them great for tasks needing exact control. For example, robots and medical tools often use optical encoders because of their high precision.
Magnetic EncodersThese measure position using magnetic fields. They are strong and work well in tough conditions. Magnetic encoders are good when dealing with dust, moisture, or vibrations.
Incremental EncodersThese create pulses as the motor moves around its shaft. The pulses show the motor’s direction and position clearly. Incremental encoders are often used to control speed in servo motors because they’re simple but effective.
Each type has its own strengths based on what you need it for. For gimbals, choosing one with both fine detail and toughness is usually best.
How Gimbal Motor Encoders Improve Accuracy
Position and Speed Feedback
A gimbal motor encoder helps by giving exact position and speed data. It watches the motor's movement and sends this information to the controller. This allows the motor to adjust quickly, keeping things steady and smooth. Without this real-time feedback, motors would have trouble staying balanced during sudden movements.
This accuracy is helpful for drones and cameras. For instance, when a drone faces strong wind, the encoder helps the motor fight back. This keeps the camera steady so it can take clear videos or photos. The encoder also makes the motor work better by avoiding extra adjustments. This saves battery power, which is important for devices with limited energy.
Reducing Mistakes and Improving Stability
Gimbal motor encoders help fix small errors in motion control. They notice tiny changes in position and correct them right away. This stops shaking or jerky movements, making everything run more smoothly. Whether you're flying a drone or filming action scenes, encoders keep your device working well.
Real-Life Example: TurboFlys Brushless Direct Drive Motor
The TurboFlys brushless direct drive motor shows how encoders improve stability and accuracy. It uses a high-quality encoder that gives detailed feedback on speed and position. This prevents problems like misalignment or drifting from happening. The system stays balanced even in tough situations.
"The TurboFlys motor proves that advanced encoders with brushless motors create amazing precision."
This example shows why picking a good encoder matters for your needs. A strong encoder not only boosts performance but also makes your equipment last longer. Whether you're a pro or just enjoy hobbies, using a reliable gimbal motor encoder gives you great results every time.
Advanced Ways to Improve Encoder Accuracy
High-Resolution Encoder Features
High-resolution encoders help make gimbal motors more accurate. They track tiny motor movements and give detailed feedback. With higher resolution, they notice small rotations and adjust precisely. This is very important for drones or cameras needing steady performance.
Optical encoders are great for high-accuracy tasks. They use light to measure motion and position with precision. Industries like robotics and aerospace trust them for tough stabilization jobs. But high resolution alone isn’t enough for full accuracy. Errors and system setup also affect how well it works.
Calibration and Software Improvements
Calibration ensures the encoder matches the motor’s real position. Without calibration, even advanced encoders can give wrong results. Regular checks fix issues from wear, heat changes, or misalignment.
Software makes encoders work even better by processing data smartly. Algorithms filter out noise and fix uneven motor movements in real-time. For example, drones with good software stay steady in rough winds. Together, calibration and smart software improve motion control greatly.
Using Both Load and Motor Encoders
Using load and motor encoders together improves gimbal accuracy a lot. A motor encoder tracks speed, while a load encoder watches the device's position, like a camera or sensor.
In gear-driven systems, this combo fixes problems like backlash errors. The load encoder finds shifts in position; the motor encoder corrects them fast. This teamwork keeps things stable even in hard conditions. Combining both types gives better results than using one alone.
Challenges and Practical Solutions
Common Problems in Improving Precision
Making gimbal motors precise with encoders can be tricky. One big problem is noise interference. Electrical noise from nearby parts can mess up encoder signals. This causes wrong feedback, leading to shaky motor movements and poor performance.
Another issue is misalignment. If the encoder and motor shaft are not lined up right, feedback becomes incorrect. This makes it hard for the motor to stay steady when working.
Over time, wear and tear also reduce precision. Using gimbal motors a lot can cause parts to wear out. Dust, moisture, and temperature changes make this happen faster, lowering system reliability.
Lastly, there's calibration drift. Without regular recalibration, even good encoders lose accuracy over time. This drift leads to uneven performance in tasks like drone flying or filming videos.
Fixes: Reducing Noise, Aligning Parts, and Maintenance
You can solve these problems with some simple steps. To fix noise interference, shield encoder cables from electrical noise. Use good-quality cables with proper grounding to avoid signal issues. Advanced software can also clean up noisy signals for better feedback.
For misalignment, install the encoder carefully so it lines up perfectly with the motor shaft. Alignment tools help during setup, and regular checks keep everything in place for smooth operation.
To handle wear and tear, clean your equipment often to remove dust or dirt. Use tough encoders like magnetic ones that work well in harsh conditions. Lubricate moving parts and check for damage to make your system last longer.
Fixing calibration drift requires regular recalibrations of your encoder system. Many modern encoders have easy calibration features built-in now. Pairing them with smart software ensures accurate adjustments during long use periods.
"Direct-drive gimbals paired with today’s encoders give amazing precision."
By following these tips, you’ll improve how well your gimbal motors work every time! Whether you're flying drones or making films, these fixes keep your gear reliable anywhere!
Gimbal motor encoders help keep systems steady and precise. They give important data about position and speed for smooth motion. Newer technologies, like high-resolution encoders, improve how they work. Calibration fixes problems like noise or misalignment in systems. For instance, direct-drive gimbals with rotary encoders are very accurate.
"Better encoder precision means reliable use and great control."
Picking the right encoder and caring for it improves stability and accuracy in tough tasks.